COLUMNコラム
ピッキングの効率を上げる5つのポイントとは
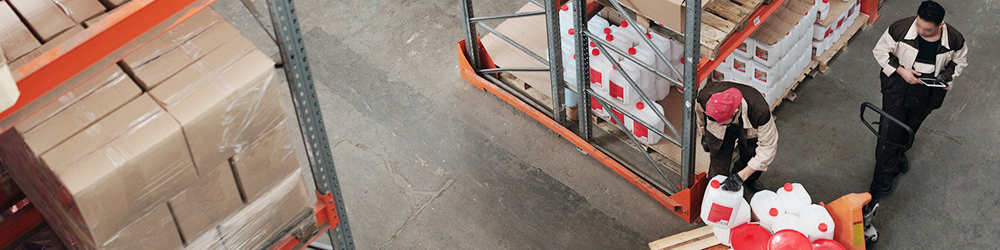
出荷のスピードを上げるため、効率的にピッキングを行いたいという方も多いのではないでしょうか?
もちろん、表示器等を利用したデジタルピッキングシステムの導入が効果的です。
しかし、ここではシステムの導入のみならず、様々な方法でピッキング効率を上げる方法をご紹介いたします
デジタルピッキングシステムの導入
リストに書かれている商品を1つ1つ確認しながらピッキングを行う一般的な方法に比べ、表示器を利用したデジタルピッキングシステムの導入は作業効率を大幅に改善することが可能になります。
表示器のライトが点灯した棚の品物を表示された数量だけピッキングするだけなので、いちいちピッキングリストを確認する必要がなくとてもスピーディーに作業が行えます。
また、無線表示器を利用することにより、ピッキングするカゴ車などをまとめて配置することが可能になりますので動線を短縮化でき、作業効率も大幅に上げることが可能になります。
出荷頻度が高い商品を出荷しやすい位置に移動
商品を出荷頻度毎にランク分けするABC分析などを行った後、出荷頻度が高い商品を出荷口の近くや出しやすい高さの棚に移動することでスムーズにピッキング作業を行うことが可能になります。
また、その際には作業者が一か所に集中し、渋滞が起こってしまわないように動線を工夫することも重要です。
作業者が覚えやすいロケーションに商品を配置
一緒に出荷する機会が多い商品を近くに配置する。同じカテゴリーの商品をまとめて1つのエリアに置いておく等ロケーションを工夫することで、商品が置いてある棚を覚えやすくなります。
いちいちリストの棚番を確認する必要がないので効果的に作業を行うことができるようになります。
適切なピッキング方法を選択
ピッキングには、発送先毎にピッキングを行うシングルピッキングと複数出荷先分の商品をまとめてピッキングするトータルピッキングがあり出荷形態に合わせて適切なピッキング方法を選択する必要があります。
一般的には出荷先は多いがアイテム数が少ない場合などにトータルピッキングが効果的だと言われています。
出荷状況や作業動線の長さなどを考慮に入れて適切に作業方法を検討することが重要になります。
適切な広さの動線を確保
保管スペースを広くしたいと思うあまり、棚と棚の間があまりにも狭く、ピッキングする際に人がすれ違ったり、追い抜いたりすることができないという倉庫も少なくないのではないでしょうか?
適切な動線の幅を確保することで、移動しやすく作業者の渋滞もなくなりますので、効果的にピッキング作業が行えるようになります。
まとめ
効率的にピッキング作業を行える環境を作ることで、出荷までのスピードが上がり物流サービスに付加価値を与えることが可能になります。
また、残業などを減らすこともできるようなりますので、無駄な人件費を抑えることもできます。
この機会に庫内作業を見直し、ピッキング効率を改善してみませんか?
また、システムによる業務の改善を検討している方。デジタルピッキングシステムへの資料請求、お問い合わせはこちらからどうぞ。
物流ソリューション一覧
アトムエンジニアリングの物流ソリューションをご紹介します
課題 | 対応方法 | ソリューション |
---|---|---|
誤出荷を防止したい | バーコード照合を活用した出荷検品の実施 | 在庫管理システム >> |
在庫の先入れ先出しをしたい | 入荷日・製造日・賞味期限などの日付をシステムで管理 | 在庫管理システム >> |
在庫管理の精度を上げたい | 倉庫作業を行う際に、ハンディターミナルなどでバーコードを照合 | 在庫管理システム >> |
商品のロット管理、賞味期限管理を行いたい | 入荷時にロットや賞味期限をシステムに登録し、履歴を管理 | 在庫管理システム >> |
バーコードを利用した出荷検品だけ行いたい | ハンディターミナルやスマートフォンを活用したバーコード検品が可能な検品システムの導入 | 検品システム >> |
トレーサビリティに対応したい | 商品の賞味期限やロット番号を管理し、出荷履歴が見えるシステムの導入 | 在庫管理システム >> |
ピッキング作業の時間を短縮したい | 表示器を使用したデジタルピッキングシステムの導入 | デジタルピッキングシステム >> |
仕分け作業の時間短縮をしたい | 表示器を使用したデジタルアソートシステムの導入 | デジタルアソートシステム >> |