COLUMNコラム
倉庫管理業務を効率化するための10のポイントとは
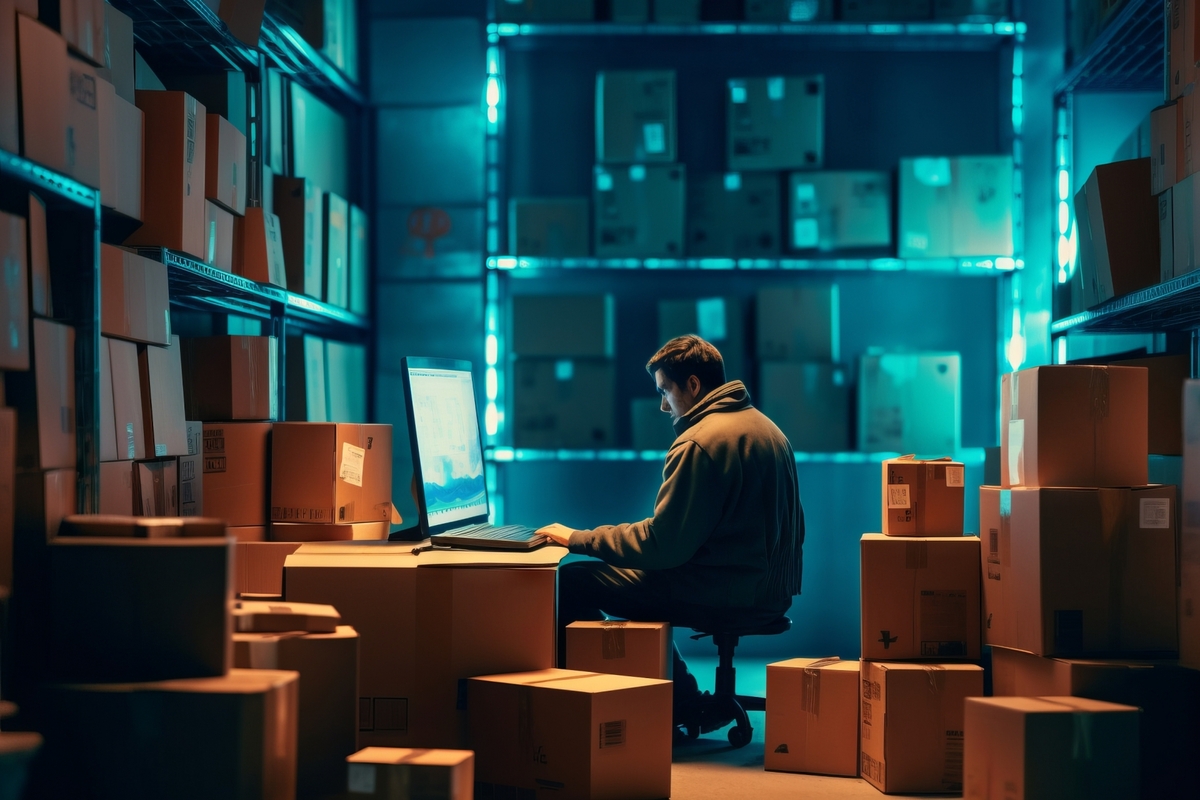
倉庫内作業が煩雑で業務が滞り、焦って作業を行うためミスが発生してしまうという悪循環に陥ってしまっている現場も多いのではないでしょうか?
今回は倉庫管理業務を効率化するための10のポイントをご紹介します。
倉庫内の5Sの徹底
倉庫内の業務を効率化するために最初に行うことは、5Sの徹底ではないでしょうか?
5Sとは下記になります。
[整理]
不要な物を処分すること
[整頓]
道具や商品などの保管場所が明確に決まっており、それらが適切な場所に保管されていること
[清掃]
掃除を定期的に行うこと。また、それが決められたルール通りに行われているか点検を行うこと
[清潔]
倉庫内が清潔な状態で保たれていること
[躾(しつけ)]
倉庫内の整理整頓や清掃が正しく行われるよう習慣づけること
どれほど、高性能なマテハン機器やソリューションを入れても、倉庫内が乱雑で何処に何が置かれているか分からないような状態では、適切に倉庫業務を行うことは難しく、ミスも発生してしまいます。
要らない物を処分し、要る物は何処に保管するかを明確にする。
整理整頓・清掃を行えるよう習慣化し、定期的にそれらが行われているかをチェックするルール作りを行うことが倉庫管理業務を効率化する第一ステップになります。
作業スペースの十分な確保
商品を保管する場所を広くするため倉庫作業を行うスペースを狭くしてしまい、効果的に業務が行えないというケースは発生しがちです。
倉庫の入出荷を行う場所が狭いと、商品を仮置きするスペースがなくなり、何度も荷物を動かすことになってしまうため、作業効率が落ちてしまいます。
また、商品を保管している棚の間が狭すぎると作業を行う際に渋滞が発生し、倉庫作業の効率を下げてしまいます。
商品を保管するスペースを広くすることも重要ですが、倉庫作業を効率的に行うためには、作業スペースを十分に確保する必要があります。
ロケーション管理の実施
商品が倉庫の何処に保管されているかを明確にするロケーション管理も重要になります。
倉庫の間口に一定のルールで英数字の番号を振り、商品を保管した際にどの間口に入れたかを管理することで、何処に何の商品が保管されているかを明確にすることができます。
これにより、倉庫作業に慣れていない方でも倉庫作業が行えるようになり、倉庫を管理しているスタッフがいないと倉庫作業が行えないという状態から脱することができます。
倉庫管理責任者の任命と業務の明確化
倉庫管理責任者を決め、どのような業務を行うのかを事前に明確にしておくことも重要になります。
これを行わないと商品発注担当者が多めに商品を発注したり、営業担当が勝手に商品を持ち出したりするなどのことが発生し、在庫管理が適切に行えなくなってしまいます。
商品の欠品が何度も発生しては、企業としての信頼も失ってしまいますし、在庫が大量に倉庫にあるような状態では、資金繰りが悪化し、キャッシュが不足。最悪は企業が倒産してしまうということもあり得ます。
倉庫の在庫数を適切に管理し、健全な企業活動を行うためにも商品の在庫管理を行う責任者を決め、その責任者が何を行うのかを明確にすることで在庫管理に関するトラブルを減らすことができます。
作業内容のマニュアル化
倉庫内作業を行う際に、各々が自分のやり方で業務を行っているよう現場では、どうしても作業ミスが発生してしまいます。
業務を行う際に、スピーディーでありながらミスが発生しない方法を検討し、それをマニュアルに落とし込む。これを作業スタッフのみんなが守ってもらうようルールを決めることで、作業の品質が一定になり、結果的に作業ミスの発生を軽減できるようになります。
人的資源の有効活用
倉庫作業において、無駄が発生してしまう原因の一つとして作業スタッフがやることがなく手待ち時間が発生してしまうことです。
このような状態にならないように、人員が多めに必要となる時間を明確にし、その時間に人員が確保できるように、勤務時間を柔軟に変更したり、商品の入荷や出荷の時間を調整するなどの対応も重要になります。
このように人的資源を適切に、必要な場所に必要な人数配置できるように事前に準備を行うことで倉庫内作業をスピーディーに行うことができるようになります。
在庫管理システムの導入
在庫管理システムを導入することで、倉庫管理業務を大幅に効率化することができます。
商品にバーコードが付いている場合には、ハンディターミナルやスマートフォンの機器でそれらを読み取ることで、手書きで作業内容をメモする必要がなくなるため作業ミスも防止でき、スピードも向上します。
また、各作業の際に商品や間口についているバーコードを読取り、それらのデータを在庫管理システムに送信することで、リアルタイム在庫管理が実現します。
在庫精度が改善し、何処に商品があるか倉庫内を探しまわる必要もなくなります。
(リアルタイム在庫管理も可能なクラウド在庫管理システムはこちら>>)
商品を保管する間口の確保
商品を保管する間口が不足すると、本来置くべきではない所に商品を保管することになるため、結果として現場が混乱し、それによりミスが発生。業務が滞ってしまいます。
このようなことにならないためにも、在庫管理システムなどで出荷頻度が低い商品を見つけ、それをまとめて保管することで間口を増やすことも効果的です。
また、在庫管理システムを活用し、商品を保管する場所を自由に変えられるフリーロケーションに変更することで、商品が現在入っていない間口も効果的に利用でき、間口数が足らないという状況を改善することができます。
倉庫内の作業動線の短縮
出荷頻度の高い商品を入出荷しやすい間口に保管するようにすることで、倉庫内作業を行う際の動線を短縮することができ、倉庫業務の効率化が実現します。
在庫管理システムの出荷ABC分析の機能などを活用し、出荷頻度が高い商品を明確にすることで、商品の保管場所を最適化することができます。
また、主にピッキングする商品を置いておくための場所(ピッキングエリア)と基本的に大きな荷姿で商品を保管しピッキングエリアへ補充をするための商品を置いておく場所(ストックエリア)に分けることで、ピッキングエリアをコンパクトにでき、さらに動線を短縮化することができます。
効率的なピッキング方法の選択
商品の種類や出荷先の件数により商品の最適なピッキング方法も変わってきます。
1オーダー毎にピッキングするオーダーピッキング(シングルピッキング)は一般的に商品の種類が多い倉庫で効率的であるとされており、作業動線は長くなりますが、ピッキングした後に仕分けをする必要がありません。
逆に複数のオーダーを1度にピッキングするトータルピッキングは出荷先数が多く、商品の種類が少ない倉庫では効果的であるとされています。
トータルピッキングでは、複数の種類の商品を一度にピッキングできるため、作業動線は短くなりますが、ピッキングした後に仕分けを行う必要があります。
実際に現場の運用に則したピッキング方法を選択することで業務の効率化が実現します。
まとめ
倉庫内作業を効率化するためには、整理整頓を行い、倉庫内作業のルールを決めることで、ミスが発生しづらくなり、作業スピードも改善できるようになります。
倉庫内作業に時間がかかり業務を改善したいと考えている方はこのコラムを参考にしていただければ幸いです。